Press Brake Forming: Shaping Metal To Your Exact Specifications
Here at Herold Precision Metals, we’ve honed our press brake forming capabilities over the last three decades, becoming synonymous with accuracy, quality, and consistency in metal fabrication. Our press brake metal forming services cater to technically complex projects, from prototypes to large-scale production runs, across industries including medical, aerospace, electronics, and more.
Our Press Brake Equipment
We've invested in a diverse range of press brakes to handle various materials, thicknesses, and project requirements. Our lineup allows us to tackle many different metal-forming tasks with precision and efficiency.
Quanity
1
2
2
1
2
3
3
2
1
3
6
2
Model
Safan Ultra
Amada 1003 ATC
Amada HFE 2204S
Amada HFE 1704S
Amada HFE 2204S
Amada HG 1303
Amada HDS 1303
Amada HFE 1003S
Amada HG 8025
Amada RG80
Amada RG5020LD
Amada EG4010 Ergonomic (2023)
Bed Size
10’
10’
14’
14’
14’
10’
8’
10’
8’
8’
6’
4’
Tonnage
130
110
240
220
220
130
130
100
80
80
50
40
Enhancing Precision and Efficiency
Our advanced ATC (Automatic Tool Change) brakes enhance efficiency by allowing seamless transitions between different tools, further supported by our extensive tooling library and advanced offline programming capabilities. This enables us to simulate your bending programs before any material is cut, streamlining both prototype and production processes while reducing costs. This approach also supports design phases, where engineering designs can be validated through the DFM (Design for Manufacturing) process. As parts transition from 2D flats to 3D forms, we ensure that critical aspects of DFM and NPI (New Product Introduction) are thoroughly validated. Our comprehensive equipment and tooling resources enable us to consistently meet your delivery requirements, ensuring that quality, cost, and delivery expectations are not only met but exceeded.
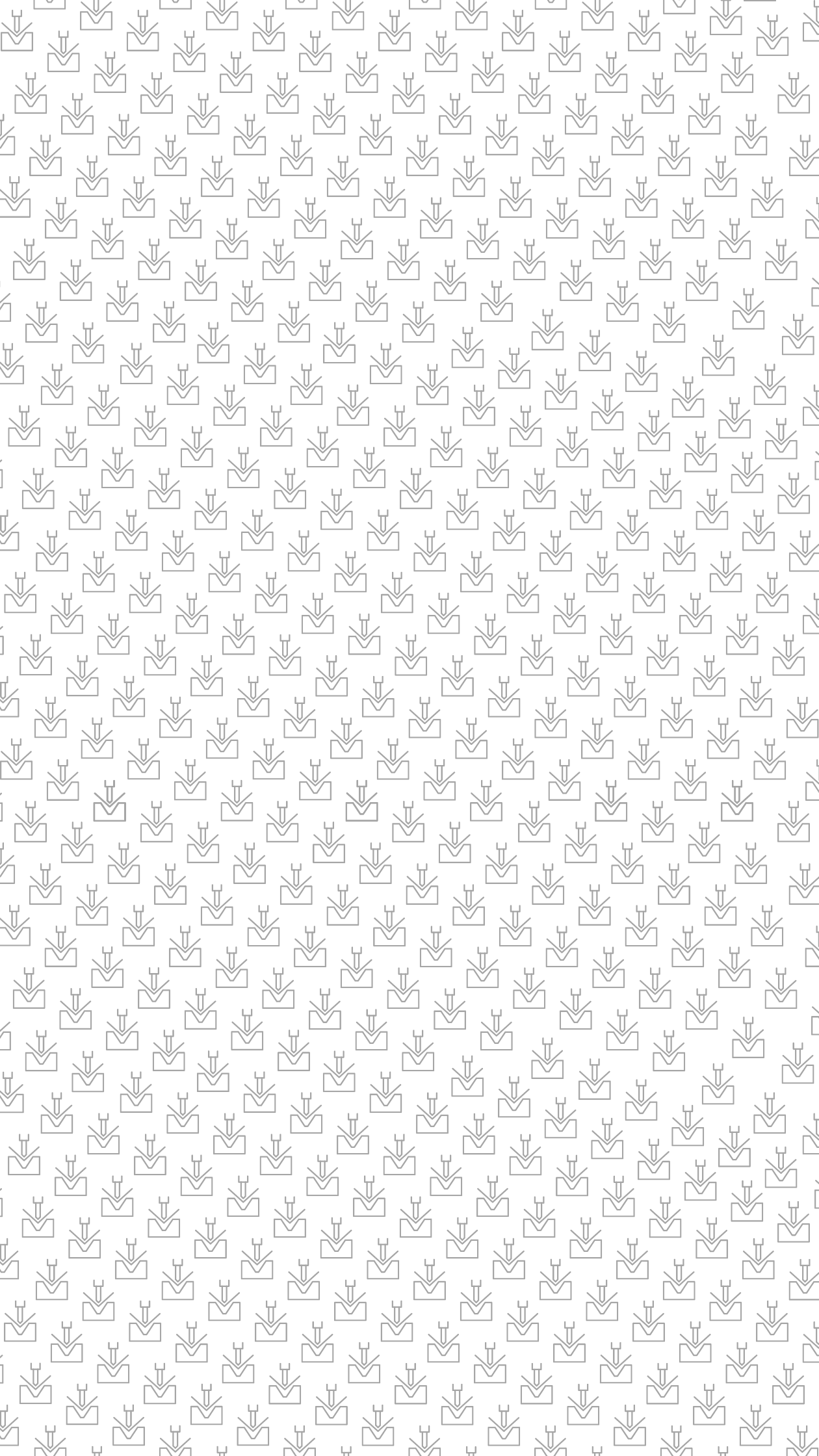
The HPM Difference
When you partner with HPM for brake press forming, you're choosing:
Advanced Simulation: Our offline programming capabilities allow us to simulate your bending programs before any material is cut. This proactive approach saves both time and costs associated with prototypes and production orders. By leveraging these simulations during the design phase, we can validate engineering designs through the Design for Manufacturability (DFM) process, ensuring accuracy before moving into production.
Tooling Capabilities: Our extensive tooling library supports the efficient transition from 2D flats to 3D parts. This vast resource allows us to meet the critical aspects of DFM and New Product Introduction (NPI) requirements, ensuring that we can accommodate your project needs and meet your delivery deadlines with precision.
Precision at Scale: We maintain exacting standards whether you need a prototype or a large production run.
Proactive Problem-Solving: Our team anticipates challenges and develops solutions before they impact your project.
Collaborative Approach: We work closely with your team, from engineers to management, to reach alignment at every stage.
Flexible Capacity: Our diverse press brake lineup allows us to scale production to meet your changing needs.
Commitment To Quality: Our reputation is built on meticulous attention to detail. We employ rigorous quality control measures, invest in continuous team training, and maintain ISO 9001:2015 certification to ensure consistent, high-quality output.
Applications And Expertise
Our press brake forming services are integral to creating:
Custom metal parts and components
Enclosures and housings
Brackets and frames
Panels and chassis
We've developed specific expertise in:
Complex part forming and bending
Integrating press brake operations with other fabrication processes
Maintaining consistency from prototype to production
Optimizing production for reduced lead times and costs
Industries HPM Serves
HPM serves a diverse array of markets, providing tailored solutions to meet the unique needs of each industry. From military and data centers to electronics and consumer goods, we leverage our press brake forming expertise to deliver high-quality products and services that exceed expectations across various sectors.
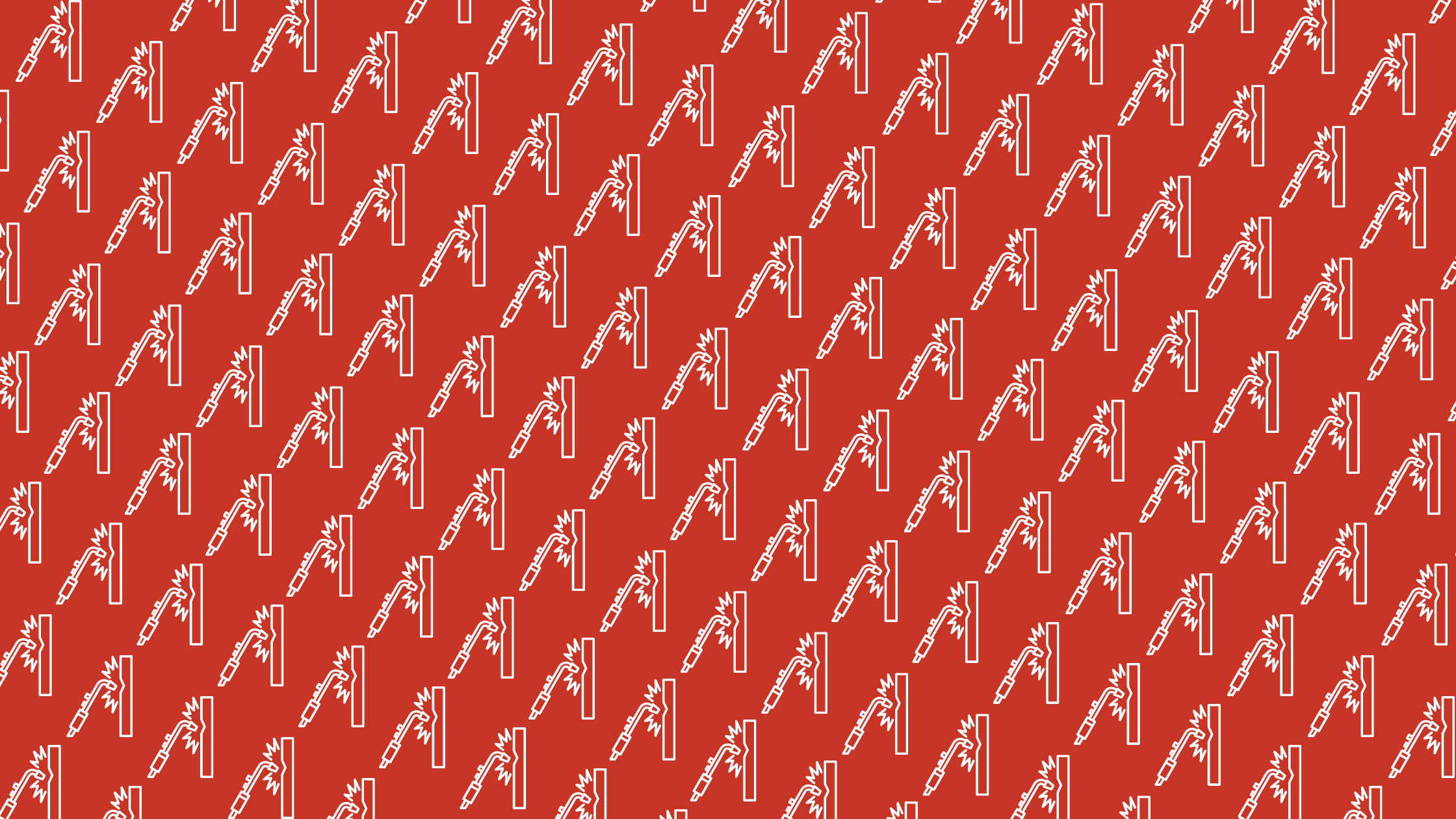
Let's Collaborate On Your Next Fabrication Project
From initial concept through production, HPM is equipped to support your project with press brake forming and a full suite of metal fabrication services. Contact us today to discuss your specific needs and receive a detailed quote.